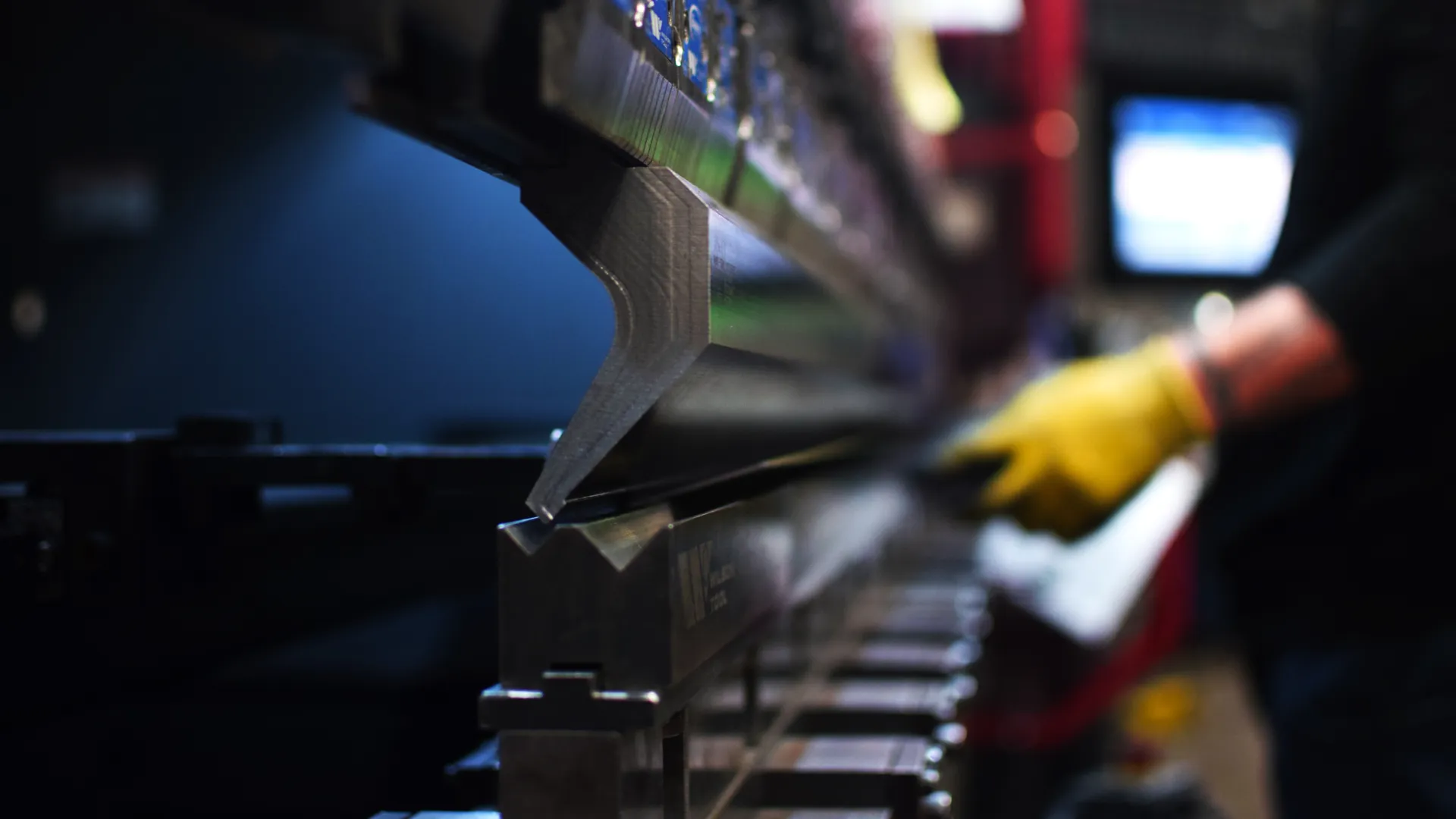
SHEET METAL FABRICATION
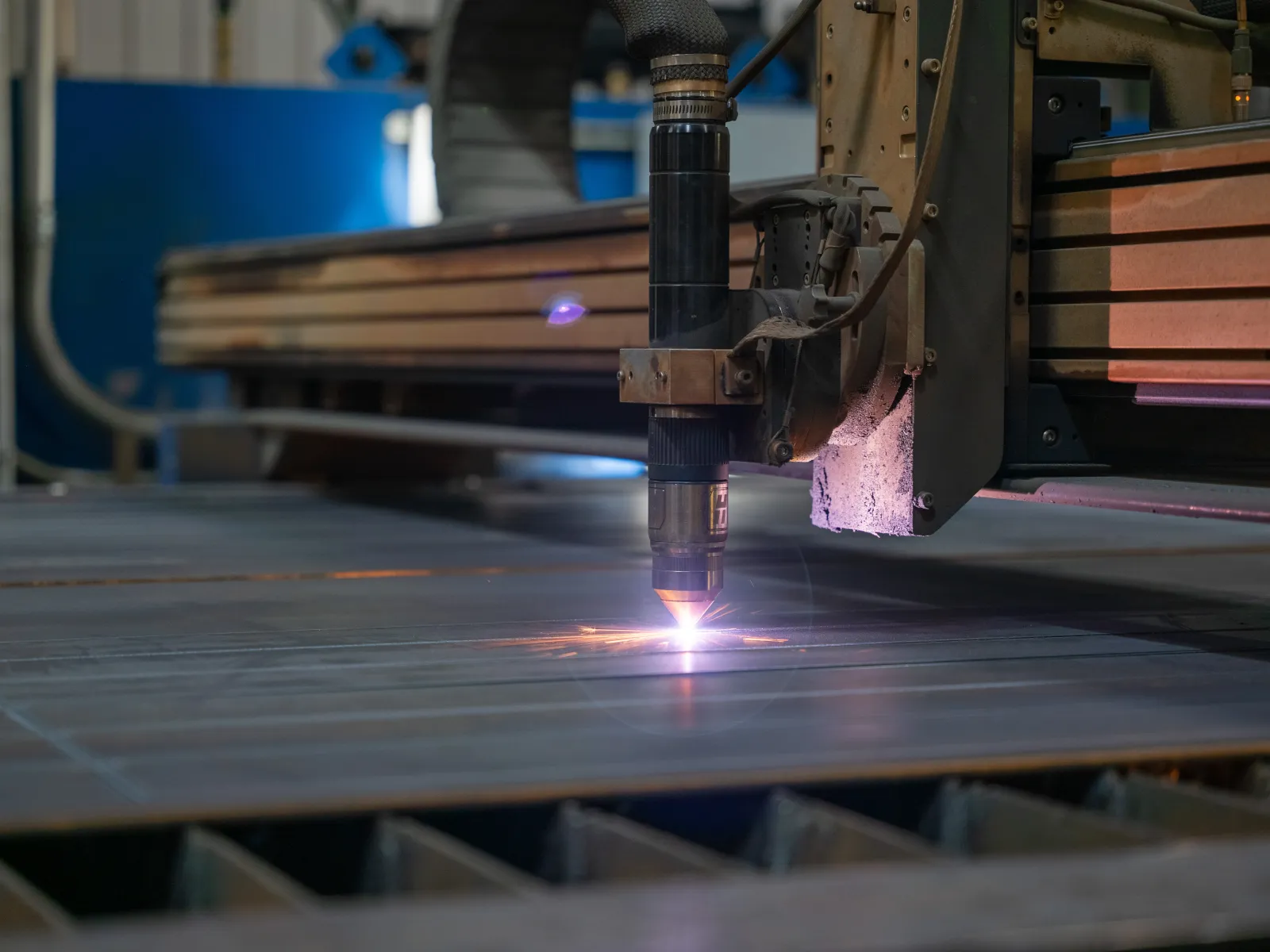
PRECISION CUTTING
We specialize in the rapid precision cutting of mild steel, stainless steel, and aluminum. We provide metal cutting as an à la carte service but excel at providing customers with a turnkey solution for cut-and-formed precision metal products, such as enclosures, frames, panels, and vents.
We cut sheet metal using primarily automated CNC lasers with integrated material stacking systems to expedite production. Our lasers can handle carbon steel up to 1" thick, stainless to 0.5" thick, and aluminum to .375" thick.
For thicker carbon steel and stainless steel plate, we use our CNC plasma-cutting table, which can handle pieces of metal up to 40' long. We also employ a CNC water jet cutting table to cleave through metal up to 6" thick and to cut other materials such as titanium, inconel, plastics, natural and manufactured stone, rubber, copper, fiberglass, and wood, when a job calls for it.
LASER CUTTING
Our laser cutting machines include a Mitsubishi ML4020NX 6000-watt laser and a Mitsubishi ML3015LVPlus 4000-watt laser. Both are attached to material stacking stations for automatic loading and unloading to optimize production. We also use NCELL automations on all of our cutting systems so that parts can be nested, conserving material and reducing costs.
PLASMA CUTTING
Our plasma cutting station includes a Messer Fineline Plasma 200 Amp table and a Koike Aronson Plasma 400 Amp high performance table. The Koike Aronson is 8' x 40' and can be used to cut sheets anywhere from 12' to 40' long.
WATER JET CUTTING
Our water jet cutting system includes two Calypso Dual Head 50 HP tables, which we use to cut thicker materials. We also use the water jet cutter for jobs where no heat-affected zone (HAZ) is permitted since the water jet cuts without interfering with the material's inherent structure.
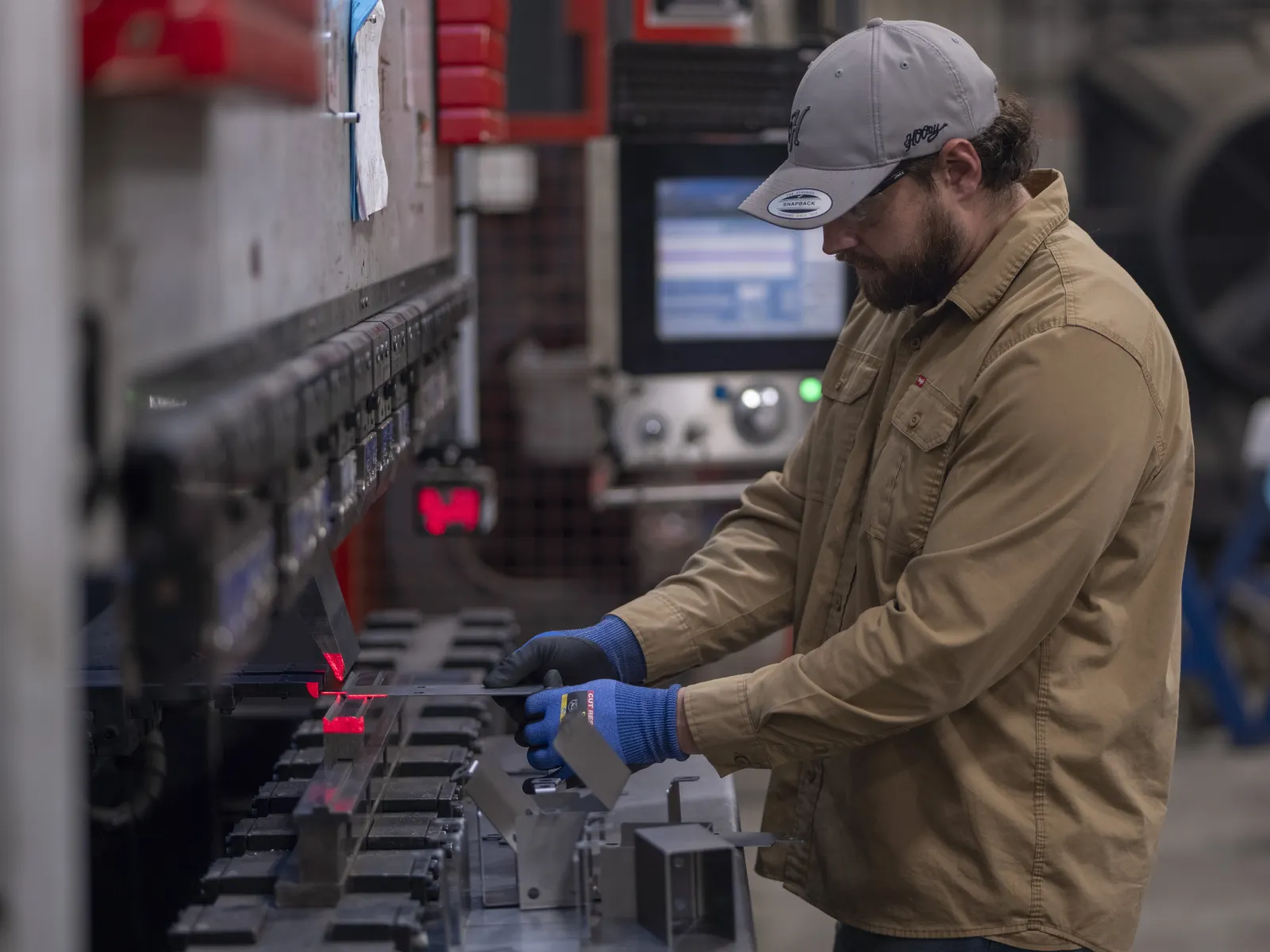
CNC FORMING
Our staff is expert at CNC forming aluminum, carbon steel, and stainless steel sheet metal. Using SolidWorks and Metamation simulation software, we quickly calculate bends and ensure that our precision forming and bending is consistently done correctly the first time.
CNC forming is ideal for quick-turnaround production orders. Using a CNC brake press to automatically position back gauges and compute optimal bend sequences, we are able to form sheet metal to fabricate up to 1,000 products at a time, keeping costs low and speeding up production for these sorts of smaller jobs that simply can't justify manufacturing traditional deep-drawn dies.
We employ CNC forming as part of simple cut-and-form jobs. CNC forming also represents an integral step in our turnkey sheet metal fabrication projects, where we take a product from design to delivery, such as the enclosures, and tanks we produce on a daily basis for a variety of industries.
We have three CNC press brakes. Our largest, a Mitsubishi Diamond Elite XL model, has bending capacity of 200 tons and a maximum bending length of 4 meters. Our two other CNC press brakes, 135 and 40 ton machines, are also Mitsubishi Diamond models that can handle sheet up to 3 meters and 1.4 meters long, respectively.
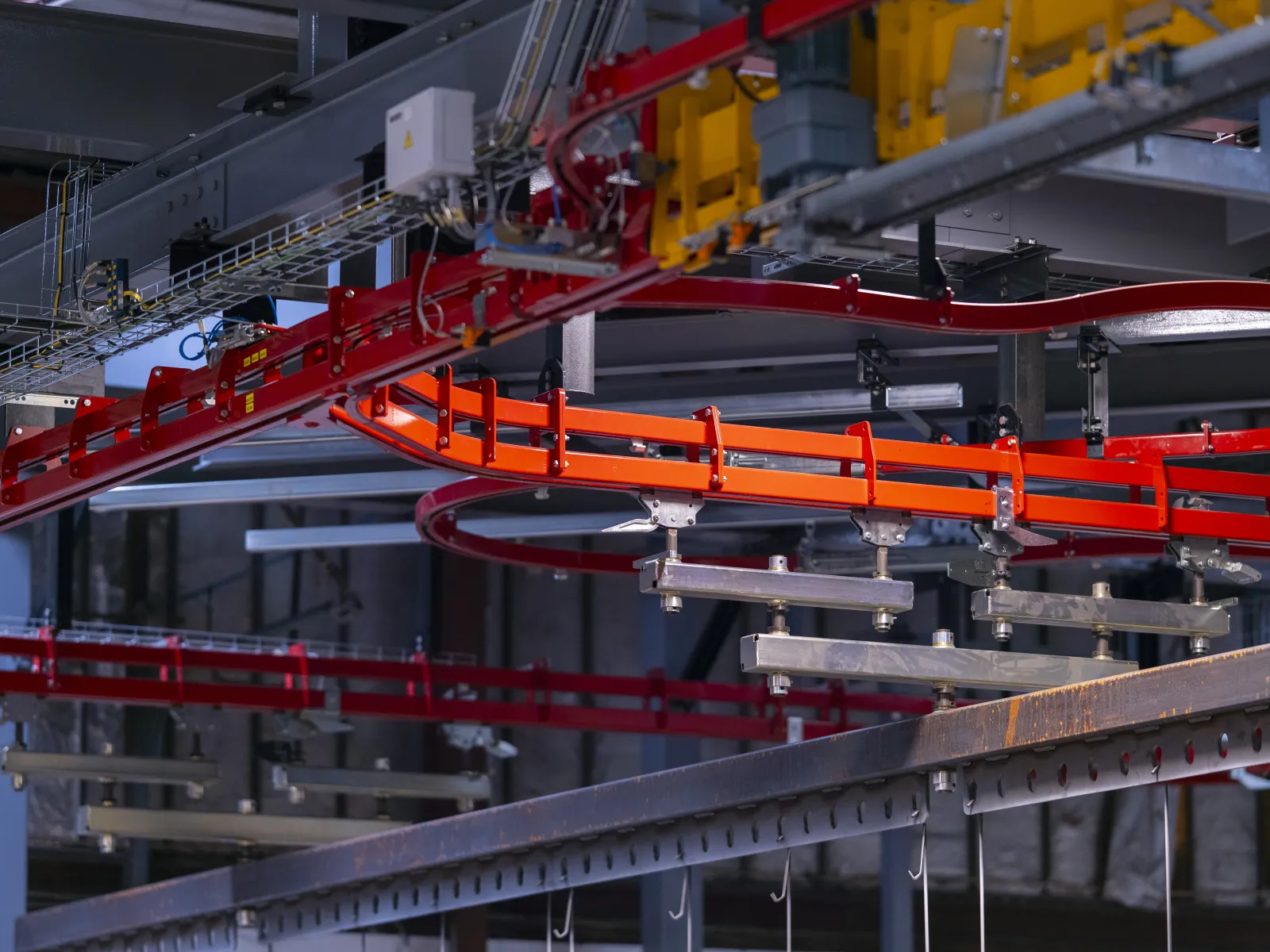
FINISHING
We take our finishing as seriously as our cutting, forming and machining, specializing in precision powder coating and food-grade stainless polishes for the sheet metal products we produce. Our quality control staff carefully monitors the thickness of the finishes we apply for all products processed in-house to ensure all finished products meet specified tolerances.
Most of the enclosures we create for the air handling and distributed power generation industries require powder coating, which our experienced staff handles entirely on site in our finishing shop. Typically, a mid-sized enclosure will take 1-2 days to finish.
Stainless products such as cut, formed, and machined metal parts for food processing, marine and medical applications are polished using our vibratory finishing mill, which eliminates much of the handwork required for proper stainless steel finishes — particularly with pipes and tubes — to expedite production.
SURFACE PREPARATION
Our in-house finishing operation employs cleaning, deburring, sandblasting, and shotblasting to prepare our products' metal surfaces at surface preparation grades anywhere from SP1 - SP10.
POWDER COATING & PAINTING
Our powder coating equipment includes an in-house powder coating booth and 20' curing oven. While powder coating is our preferred finishing method, we also offer in-house painting services.
POLISHING
Our vibratory finishing mill can process thousands of parts per day to the finest-grade stainless-steel standards. Food-grade steel finishes (No. 4) are standard for food-related products. Dairy applications require a finer finish (No. 4A), which is also available.
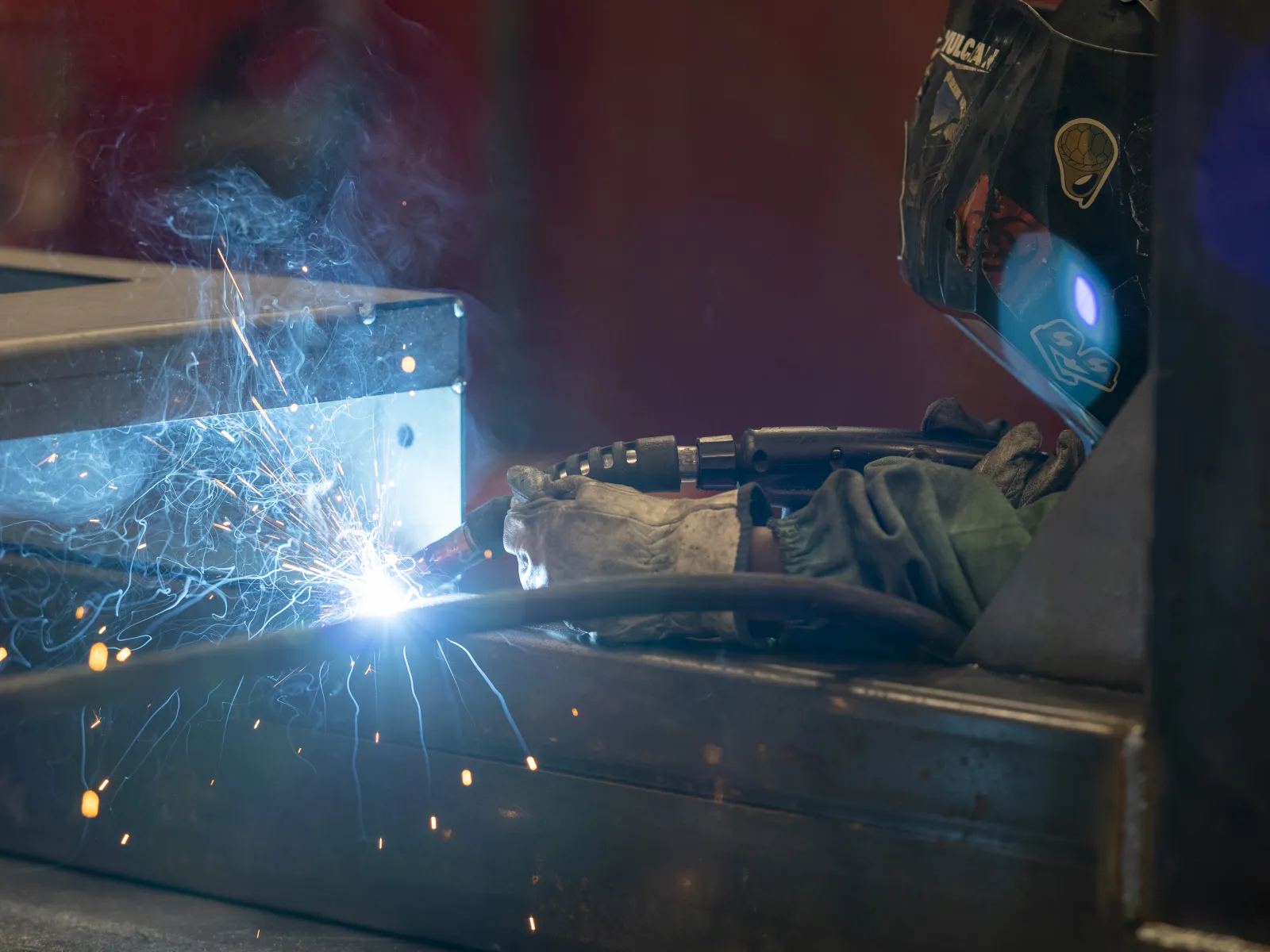
WELDING AND ASSEMBLY
Whether your job includes multiple welds or thousands of parts, our welding and assembly equipment and staff will deliver quality parts, sub-assemblies, and assemblies in record time.
For larger quantities of carbon steel, stainless steel, or aluminum products, our robotic welding system offers a cost-effective, time-saving solution. Providing top-notch weldments quickly, it can process hundreds of parts in hours.
For smaller jobs that can't justify the time and expense required to set up our robotic welding system, we also have skilled MIG and TIG welders on staff. Focused on quality and speed, our experienced welders can weld carbon steel, stainless steel, and aluminum to any standard.
ROBOTIC WELDING
Specifically, our robotic welding system is a Fusion Arc 300C three-station weld cell with a 6-axis Almega robotic welding arm. We originally acquired it to mass manufacture metal boxes used to house hydraulics system for minesweepers but today use it for a wide variety of projects.
MIG & TIG WELDING
For MIG welding, we can weld sheet metal anywhere from 22GA to ½" thick. For TIG welding, our machine of choice is a Miller Dynasty 350, which can weld aluminum up to ⅝" thick.
PIPE CUTTING AND FITTING
We perform rapid, precision pipe cutting and coping for metal pipes and tubes used in compressed air systems and drilling for oil and gas.
Producing extraordinarily clean and quick cuts, our CNC orbital plasma pipe cutting system meets tight tolerances for all pipe cutting jobs, including those involving aluminum and stainless steel pipe anywhere from 4" to 16" in diameter and up to 21' long.
Our programmable pipe cutter also streamlines our precision pipe coping, performing hillside, hole, lateral, miter, and saddle cuts with the push of a button. Exact and fast, the CNC machine allows us to skip time-consuming manual calculations and setups so we can deliver pipes ready for fit-up and welding in a fraction of the time it takes other vendors.
Our team of skilled welders has no problem welding the pipes we've precision cut using either MIG or TIG welding techniques holding tight tolerances.
PIPE COPING
For pipe coping, we use a Bug-O Systems programmable 100-amp pipe cutter, which uses a plasma cutter to cut pipe consistently to within thousandths of an inch of specifications. Equipped with an extended bed, it can accommodate pipes up to 20' long that are anywhere from 4" to 16" in diameter.
The Bug-O's pre-programmed shapes for coping include hillside, hole, miter, lateral, and saddle cuts, which can be accomplished quickly, easily, and precisely by simply specifying the requisite diameter of the cut.
PIPE WELDING
For pipe welding, our skilled welding staff relies on Miller Pipeworx machines featuring dual wire feeders. With pedal shifters that toggle between two pulsed MIG and TIG settings and geometries that allow for precision welding even when out of position (allowing us to avoid extra fixturing), these machines helps expedite our pipe welding process.